Lean process tools have a demonstrated track record of resulting in continuous improvement for manufacturing facilities. This is true regardless of the industry. Not every organization has invested in training lean six-sigma personnel but many have, and those that have not hopefully are able to utilize trained personnel from external resources. Lean manufacturing focuses on process flow, and waste issues, which is complemented by Six Sigma which focuses on variation and design. Together these are often lumped into ‘Lean Manufacturing Practices’ or ‘Quality Systems’ within a business. The basic methodology can be applied to all digitization projects and is a basis for how VESL has executed successful digital transformation projects to reverse the direction of declining factories, and improve operations resulting in millions of dollars in cost savings and avoidance.
A key challenge is how to get participation in continuous improvement programs within businesses. Many individuals are working to solve problems, but few are equipment with expertise in statistical analysis, especially as the growth of data availability has increased. Some facilities can hire teams of data scientists and engineers to work though these challenges, however most facilities are not. Furthermore, that team’s time may be allocated to other projects and not able to meet all the fluctuations in demand for statistical analysis, machine learning, data cleaning, and classification. No reasonable facility staff for peak loading in these areas.
The facility may also employ a team of ‘modelers’ who are tasked with the development of digital twins. This requires individuals with both expertise in programming, simulation, process controls, and advanced numerical physics modeling. The culmination of the work ideally results in a full digital twin.
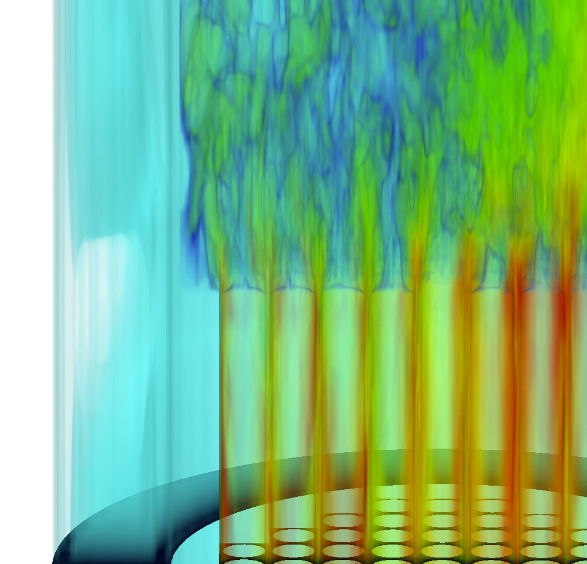
Image of Evaporation/Concentrator Separation process utilize to drive chemical reactions and separate material streams.