Continuously improving
your bottom line.
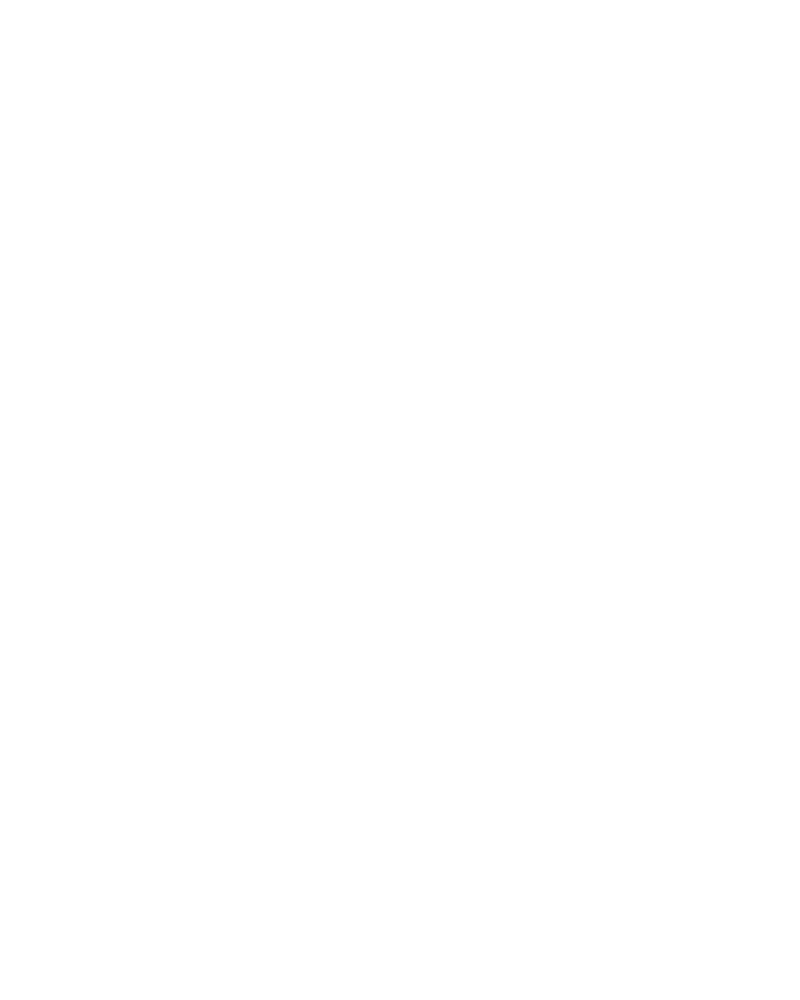
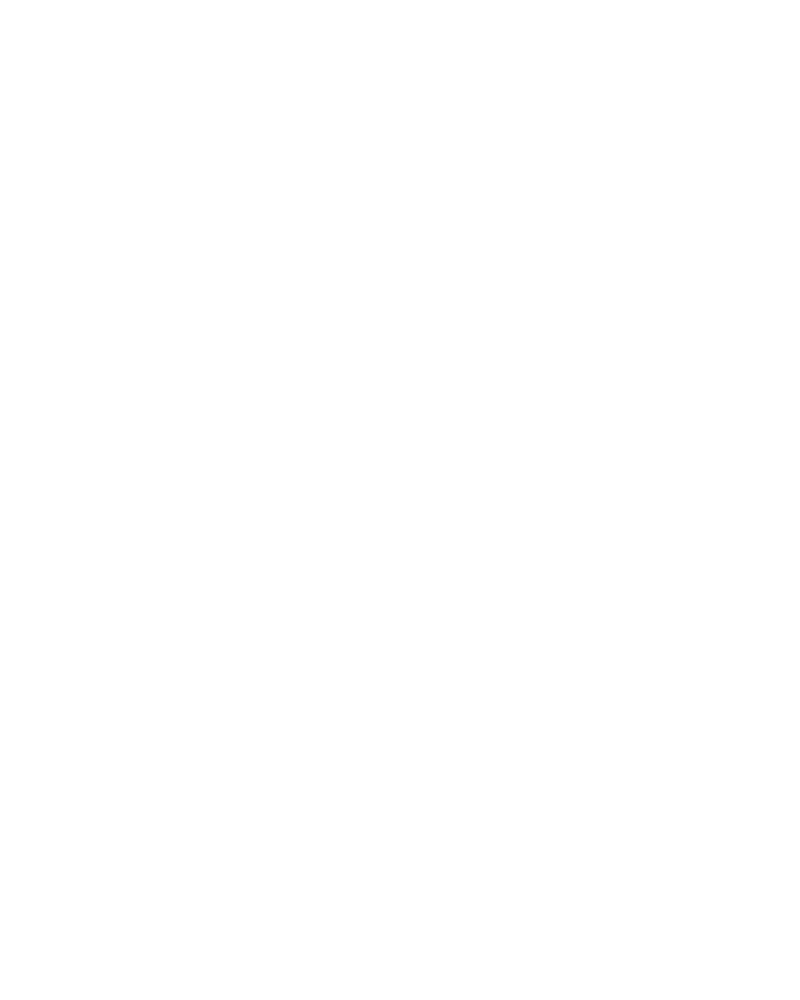
Highly Specialized
Boutique Consulting Firm
Built For Engineers by Engineers
Modern Manufacturing Struggles
Manufacturers today are grappling with a myriad of technological challenges that are impacting their operations and competitiveness.
Digital Transformation, including such things as Data Management and Analytics, Cybersecurity and Internet of Things (IoT).
Automation and Robotics, which require a highly skilled workforce to operate and maintain.
Supply Chain Disruptions, which require real time visibility and predictability to avoid.
Rapid Product Development Cycles to meet ever changing customer preferences and needs.
Sustainability and the Environment – improving energy efficiency and reducing waste in all forms while meeting all regulatory requirements.
Emerging Technologies such as AI (Artificial Intelligence)
“Brain Drain” which is occurring at an alarming rate due to an aging workforce and difficulties finding skilled replacements.
Where We Come In
We specialize in creating custom solutions to optimize both operations and R&D, helping companies overcome inefficiencies while simultaneously moving them forward in technology.
Process Development & Optimization
Modeling & Simulation
Data Science & Analytics
Industrial Automation & Control
R&D Improvement
Why Choose Us
Unlike others who focus solely on coding or PLC programming, VESL integrates advanced technology with hands-on experience to deliver real, impactful results that drive innovation and efficiency.
VESL stands out by going beyond conventional methods with our innovative “Virtual Factory” approach. This digital twin technology allows us to simulate and refine manufacturing processes before real-world implementation, giving our clients a competitive edge.
Let's Get Started
Contact us and we will work with you to develop a custom solution to save you both time and money, and keep your company competitive in this increasingly competitive space.